
Conjet
Hydrodemolition
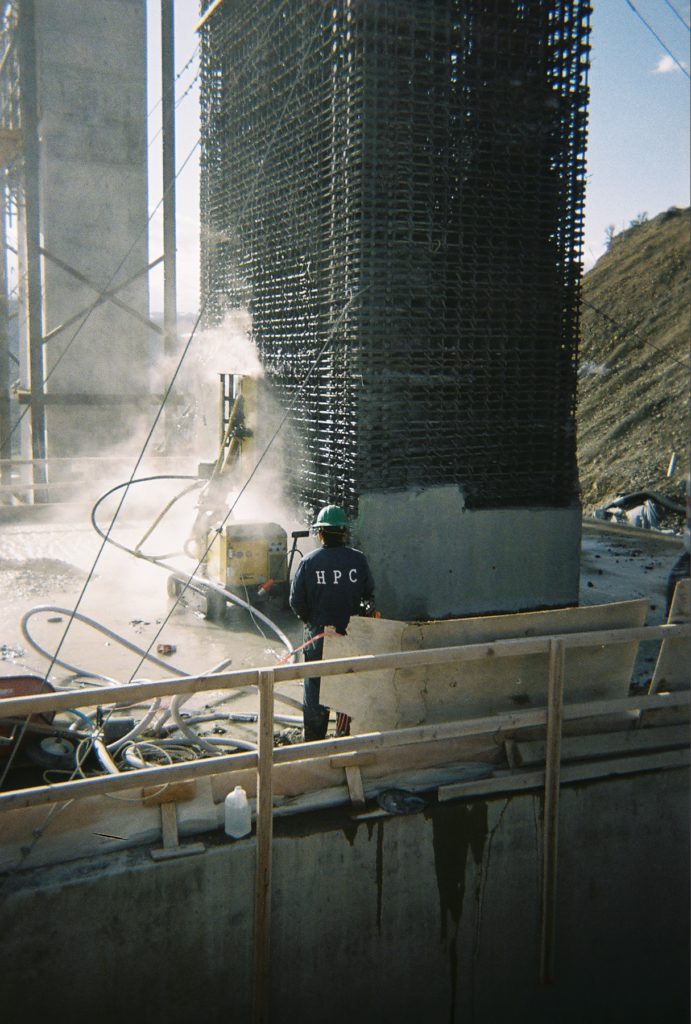
Hydrodemolition is a precisely controllable, fast and extremely efficient method of concrete removal that will not damage the surrounding structure or rebar. First developed in the 1970s, this technology has become the gold standard for concrete removal and surface preparation.
First developed in Europe, hydrodemolition has since become an accepted method for concrete demolition throughout the world. The hydrodemolition process, using high-pressure water to remove concrete, is used in the rehabilitation of parking structures, bridge decks, highway overpasses, dams and industrial concrete structures.
Hydrodemolition is often preferred over conventional removal techniques such as jack-hammering because of its higher production rates, lower noise level and superior surface for new concrete overlay to bond with. Since hydrodemolition does not cause structural vibrations, a hydrodemolition machine can remove a specific depth of concrete without producing microfractures in the remaining substrate. Further studies are showing how bridge deck repairs done with hydrodemolition methods are lasting twice as long as repairs where the demolition is done with impact tools due to the superior bonding afforded from the surface left from hydrodemolition. Independent laboratory tests have shown that the shear and pull off strengths may be as much as 300% higher in a hydrodemolished surface compared to a jack-hammered surface.
Concrete removal performed with pneumatic hammers typically produces microfractures in the upper parts of the remaining substrate. These cracks reduce bond strengths and are likely to contribute to premature delamination of repair materials. Additionally, due to the oscillating head on the Conjet robots hydrodemolition removes concrete from behind reinforcing bars as the head traverses the beam changing blasting at compound angles at the end of each traverse. Simultaneously, the rebar is cleaned by the high-velocity water and fine aggregate particles from the demolished concrete providing a wet sandblast that removes rust and bonded mortar from the rebar.
Water Pressure: 40K vs. 20K
Hydrodemolition using 36,000 to 40,000 PSI water pressure is classified as hydro-milling. Meaning at this pressure there is no regard for compressive strength of concrete. If you are to remove 2 inches it does a good job as far as consistency of depth. Much slower than 20K of course as higher pressures use less water.
Hydrodemolition using 15,000 to 20,000 PSI water pressure is more suited to the compressive strength of the concrete. There is a general rule of thumb in the industry that it takes 3.5 times the water pressure to one time the compressive strength to selectively remove concrete. So if you have 5,000 psi concrete it is effectively removed at a pressure of around 17,500 psi. Any concrete of lesser strength is also removed to the depth of the original strength concrete.
This is known as selective removal where the lower water pressures seek out the weaker or inferior concrete and leave the sound or good concrete. Once you have the water pressure set to overcome the compressive strength of the concrete by adding more flow you effectively increase productivity. More water at the same pressure sets the machine up to go faster. I.E., if you remove 50 feet per hour with 30 gallons per minute add an additional 30 gallons per minute and remove 100 feet at the same time, leaving the pressure setting the same.
Theoretically when you do a concrete removal job there will be a minimum depth of removal usually in accordance with the material being put back. Most all repair mortars or concrete specify a minimum depth or thickness for their product. This factor generally determines the minimum depth of removal if they are not increasing the grade or the width if it happens to be a vertical surface. This is done without regard for the condition of the material being removed. So if the equipment is calibrated to remove the minimum depth of good material and the weaker concrete is removed as a by product, means a better repair as we can find the bad material with this “selective removal”. Ultra high(36 – 40K) can not do this.
We at HPC are the West Coast experts in waterblasting, using water-jetting equipment and techniques since 1980. The HPC Team has worked with major contractors on projects ranging from the Hoover Dam; Hyperion Wastewater Plant; Summit Reservoir in The Bay Area; Interstate Highway projects for the California DOT, Hawaii DOT, Nevada DOT and many more. We look forward to working with you on your next project.
Hydrodemolition Job Site Benefits
Increased Productivity – Increased speed of concrete removal reduces construction time: the productivity of a 500 hp pump and robot equals that of 10-12 jackhammers, approximately 1-4 cubic yards per hour.
Low Impact – When compared to other mechanical means, hydrodemolition noise emissions are minimal, and dust clouds are eliminated. The low impact of hydrodemolition can accommodate a greater range of job-site conditions and/or limitations.
Increased Safety and Lower Labor – Robotic units remotely operated eliminate worker health hazards, increasing safety and lowering labor costs.
Versatile Applications – Hydrodemolition can be used for horizontal, vertical, and overhead concrete removal and surface preparation on reinforced and non-reinforced structures.
Hydrodemolition Applications
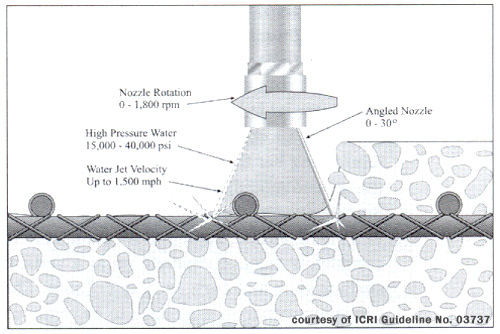
1. Full Depth Removal – Hydrodemolition can be used for full depth removal where delamination has occurred in the lower mat of reinforcing steel, or chloride contamination exists throughout the entire thickness of the slab. Although conventional removal methods can damage reinforcing steel, hydrodemolition can affect full depth removal can be safely used along expansion joints, and to expose other structural elements such as shear connectors, shear studs, and steel beam flanges.
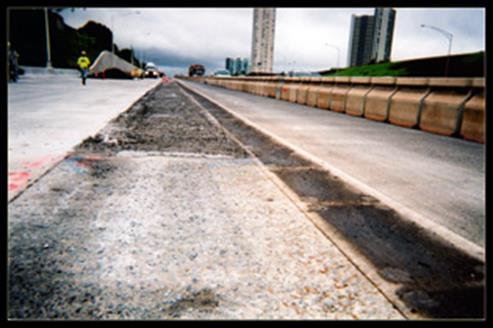
2. Partial Depth Removal – Partial depth removal is commonly required if chloride contamination has reached the top mat of reinforcing steel, or if deterioration, delamination, or spalling occurs within the top mat of reinforcing steel. Partial depth concrete removal can expose the top mat of reinforcing steel and provide clearance, typically a minimum of ¾ in. below the bottom reinforcing bar of the top mat.
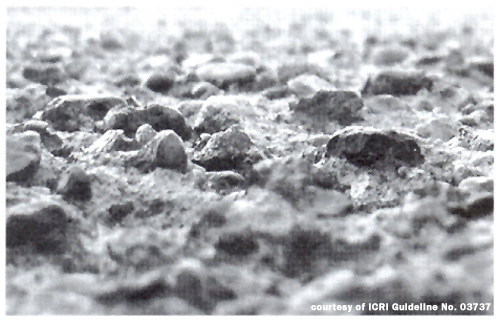
3. Scarification – Scarification is performed to remove the surface concrete and provide a rough profile. Hydrodemolition down to the coarse aggregate removes all concrete micro-fractures and damaged or crushed aggregate from any previous rotomilling and prepares the surface for concrete overlay.
Hydrodemolition Structural Benefit
Superior Bonding – Hydrodemolition creates a rough, irregular surface profile, providing an excellent mechanical bond for repair. The exposed aggregate of a water-jetted surface has much greater bonding area than that of jackhammers or sandblasting. Independent “pull off” tests have shown the bonding strength as much as 50% or higher, than that of a surface prepared with jackhammers or other mechanical methods.
Eliminates Substrate Micro-Fractures – Hydrodemolition is impact free, avoiding vibrations that loosen rebar and cause micro fractures, protecting the integrity of the substrate.
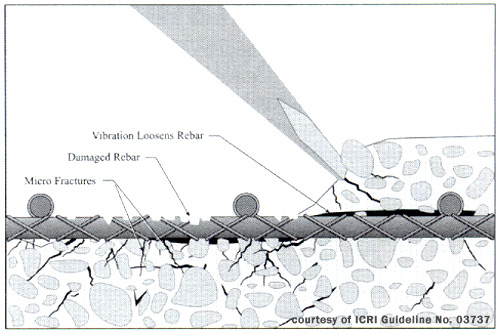
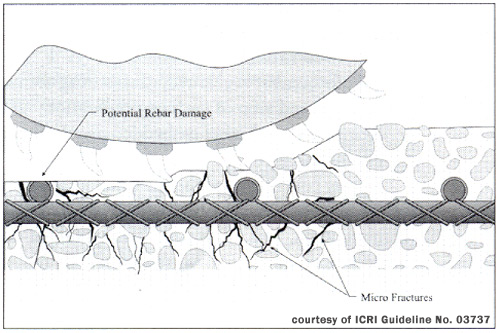
Selective Removal – A jet of high pressure water can be specifically targeted to sections of lower strength and deteriorated concrete, removing only unsound material.
Rebar Is Cleaned Without Damage – Hydrodemolition removes rust and scale from rebar, leaving intact surface.
Independent “pull off” tests have shown the bonding strength as much as 300% or higher, than that of a surface prepared with jackhammers or other mechanical methods. Hydrodemolition can be used for localized removals where deterioration is confined to small areas and for large area removals in preparation for a bonded overlay. This technology can also be used to remove existing coatings from concrete.
Hydrodemolition can be used for horizontal, vertical, and overhead concrete removal and surface preparation on reinforced and non-reinforced structures.